Automotive
New Analysis Shows Just How Bad Electric Trucks Are For Business
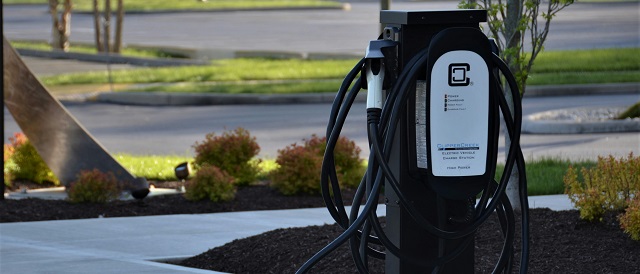
From the Daily Caller News Foundation
By WILL KESSLER
Converting America’s medium- and heavy-duty trucks to electric vehicles (EV) in accordance with goals from the Biden administration would add massive costs to commercial trucking, according to a new analysis released Wednesday.
The cost to switch over to light-duty EVs like a transit van would equate to a 5% increase in costs per year while switching over medium- and heavy-duty trucks would add up to 114% in costs per year to already struggling businesses, according to a report from transportation and logistics company Ryder Systems. The Biden administration, in an effort to facilitate a transition to EVs, finalized new emission standards in March that would require a huge number of heavy-duty vehicles to be electric or zero-emission by 2032 and has created a plan to roll out charging infrastructure across the country.
“There are specific applications where EV adoption makes sense today, but the use cases are still limited,” Karen Jones, executive vice president at Ryder, said in an accompanying press release. “Yet we’re facing regulations aimed at accelerating broader EV adoption when the technology and infrastructure are still developing. Until the gap in TCT for heavier-duty vehicles is narrowed or closed, we cannot expect many companies to make the transition, and, if required to convert in today’s market, we face more supply chain disruptions, transportation cost increases, and additional inflationary pressure.”
Due to the increase in costs for businesses, the potential inflationary impact on the entire economy per year is between 0.5% and 1%, according to the report. Inflation is already elevated, measuring 3.5% year-over-year in March, far from the Federal Reserve’s 2% target.
Increased expense projections differ by state, with class 8 heavy-duty trucks costing 94% more per year in California compared to traditional trucks, due largely to a 501% increase in equipment costs, while cost savings on fuel only amounted to 52%. In Georgia, costs would be 114% higher due to higher equipment costs, labor costs, a smaller payload capacity and more.
The EPA also recently finalized rules mandating that 67% of all light-duty vehicles sold after 2032 be electric or hybrid. Around $1 billion from the Inflation Reduction Act has already been designated to be used by subnational governments in the U.S. to replace some heavy-duty vehicles with EVs, like delivery trucks or school buses.
The Biden administration has also had trouble expanding EV charging infrastructure across the country, despite allotting $7.5 billion for chargers in 2021. Current charging infrastructure frequently has issues operating properly, adding to fears of “range anxiety,” where EV owners worry they will become stranded without a charger.
Automotive
America’s EV Industry Must Now Compete On A Level Playing Field
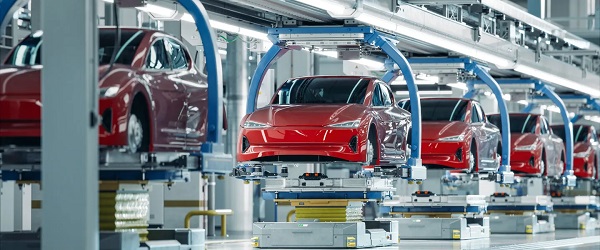
From the Daily Caller News Foundation
America’s carmakers face an uncertain future in the wake of President Donald Trump’s signing of the One Big Beautiful Bill Act (OBBBA) into law on July 4.
The new law ends the $7,500 credit for new electric vehicles ($4,000 for used units) which was enacted as part of the 2022 Inflation Reduction Act as of September 30, seven years earlier than originally planned.
The promise of that big credit lasting for a full decade did not just improve finances for Tesla and other pure-play EV companies: It also served as a major motivator for integrated carmakers like Ford, GM, and Stellantis to invest billions of dollars in capital into new, EV-specific plants, equipment, and supply chains, and expand their EV model offerings. But now, with the big subsidy about to expire, the question becomes whether the U.S. EV business can survive in an unsubsidized market? Carmakers across the EV spectrum are about to find out, and the outlook for most will not be rosy.
These carmakers will be entering into a brave new world in which the market for their cars had already turned somewhat sour even with the subsidies in place. Sales of EVs stalled during the fourth quarter of 2024 and then collapsed by more than 18% from December to January. Tesla, already negatively impacted by founder and CEO Elon Musk’s increased political activities in addition to the stagnant market, decided to slash prices in an attempt to maintain sales momentum, forcing its competitors to follow suit.
But the record number of EV-specific incentives now being offered by U.S. dealers has done little to halt the drop in sales, as the Wall Street Journal reports that the most recent data shows EV sales falling in each of the three months from April through June. Ford said its own sales had fallen by more than 30% across those three months, with Hyundai and Kia also reporting big drops. GM was the big winner in the second quarter, overtaking Ford and moving into 2nd place behind Tesla in total sales. But its ability to continue such growth absent the big subsidy edge over traditional ICE cars now falls into doubt.
The removal of the per-unit subsidies also calls into question whether the buildout of new public charging infrastructure, which has accelerated dramatically in the past three years, will continue as the market moves into a time of uncertainty. Recognizing that consumer concern, Ford, Hyundai, BMW and others included free home charging kits as part of their current suites of incentives. But of course, that only works if the buyer owns a home with a garage and is willing to pay the higher cost of insurance that now often comes with parking an EV inside.
Decisions, decisions.
As the year dawned, few really expected the narrow Republican congressional majorities would show the political will and unity to move so aggressively to cancel the big IRA EV subsidies. But, as awareness rose in Congress about the true magnitude of the budgetary cost of those provisions over the next 10 years, the benefit of getting rid of them ultimately subsumed concerns about the possible political cost of doing so.
So now, here we are, with an EV industry that seems largely unprepared to survive in a market with a levelized playing field. Even Tesla, which remains far and away the leader in total EV sales despite its recent struggles, seems caught more than a little off-guard despite Musk’s having been heavily involved in the early months of the second Trump presidency.
Musk’s response to his disapproval of the OBBBA was to announce the creation of a third political party he dubbed the American Party. It seems doubtful this new vanity project was the response to a looming challenge that members of Tesla’s board of directors would have preferred. But it does seem appropriately emblematic of an industry that is undeniably limping into uncharted territory with no clear plan for how to escape from existential danger.
We do live in interesting times.
David Blackmon is an energy writer and consultant based in Texas. He spent 40 years in the oil and gas business, where he specialized in public policy and communications.
Automotive
Federal government should swiftly axe foolish EV mandate
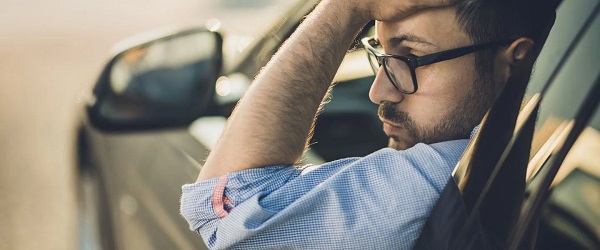
From the Fraser Institute
Two recent events exemplify the fundamental irrationality that is Canada’s electric vehicle (EV) policy.
First, the Carney government re-committed to Justin Trudeau’s EV transition mandate that by 2035 all (that’s 100 per cent) of new car sales in Canada consist of “zero emission vehicles” including battery EVs, plug-in hybrid EVs and fuel-cell powered vehicles (which are virtually non-existent in today’s market). This policy has been a foolish idea since inception. The mass of car-buyers in Canada showed little desire to buy them in 2022, when the government announced the plan, and they still don’t want them.
Second, President Trump’s “Big Beautiful” budget bill has slashed taxpayer subsidies for buying new and used EVs, ended federal support for EV charging stations, and limited the ability of states to use fuel standards to force EVs onto the sales lot. Of course, Canada should not craft policy to simply match U.S. policy, but in light of policy changes south of the border Canadian policymakers would be wise to give their own EV policies a rethink.
And in this case, a rethink—that is, scrapping Ottawa’s mandate—would only benefit most Canadians. Indeed, most Canadians disapprove of the mandate; most do not want to buy EVs; most can’t afford to buy EVs (which are more expensive than traditional internal combustion vehicles and more expensive to insure and repair); and if they do manage to swing the cost of an EV, most will likely find it difficult to find public charging stations.
Also, consider this. Globally, the mining sector likely lacks the ability to keep up with the supply of metals needed to produce EVs and satisfy government mandates like we have in Canada, potentially further driving up production costs and ultimately sticker prices.
Finally, if you’re worried about losing the climate and environmental benefits of an EV transition, you should, well, not worry that much. The benefits of vehicle electrification for climate/environmental risk reduction have been oversold. In some circumstances EVs can help reduce GHG emissions—in others, they can make them worse. It depends on the fuel used to generate electricity used to charge them. And EVs have environmental negatives of their own—their fancy tires cause a lot of fine particulate pollution, one of the more harmful types of air pollution that can affect our health. And when they burst into flames (which they do with disturbing regularity) they spew toxic metals and plastics into the air with abandon.
So, to sum up in point form. Prime Minister Carney’s government has re-upped its commitment to the Trudeau-era 2035 EV mandate even while Canadians have shown for years that most don’t want to buy them. EVs don’t provide meaningful environmental benefits. They represent the worst of public policy (picking winning or losing technologies in mass markets). They are unjust (tax-robbing people who can’t afford them to subsidize those who can). And taxpayer-funded “investments” in EVs and EV-battery technology will likely be wasted in light of the diminishing U.S. market for Canadian EV tech.
If ever there was a policy so justifiably axed on its failed merits, it’s Ottawa’s EV mandate. Hopefully, the pragmatists we’ve heard much about since Carney’s election victory will acknowledge EV reality.
-
Also Interesting2 days ago
9 Things You Should Know About PK/PD in Drug Research
-
Business2 days ago
Cannabis Legalization Is Starting to Look Like a Really Dumb Idea
-
Bruce Dowbiggin2 days ago
The Covid 19 Disaster: When Do We Get The Apologies?
-
Media2 days ago
CBC journalist quits, accuses outlet of anti-Conservative bias and censorship
-
Business2 days ago
Carney government should recognize that private sector drives Canada’s economy
-
Alberta2 days ago
Fourteen regional advisory councils will shape health care planning and delivery in Alberta
-
Alberta1 day ago
Alberta school boards required to meet new standards for school library materials with regard to sexual content
-
Business1 day ago
UN’s ‘Plastics Treaty’ Sports A Junk Science Wrapper